Metal additive manufacturing has come a long way, and there is no doubt that it will become a key enabling technology across a wide range of sectors. In recent years, revenues have grown, notable new entrants have emerged, investments have been significant, and material portfolios have broadened. The challenge with making business or design case comparisons between additive manufacturing (AM) and more established processes is the speed with which AM is advancing. It is no longer accurate to characterize AM as a single method. Especially in the metals space, an extensive list of unique processes has emerged that all fit under the additive umbrella.
A new, disruptive technology named Laser Metal Deposition – Wire Powder (LMD-WP) has been developed. LMD refers to a welding process where a material is introduced into a melt pool created by a high-power laser. LMD falls into the range of directed-energy deposition (DED) processes. Typically, the filler material introduced is a powder and is injected through a conical ring nozzle around the laser beam. The added material creates a weld bead, which then coats the underlying metal. Compared to other types of welding, LMD results in a smaller heat-affected zone, lower dilution, and lower residual stresses in the components.
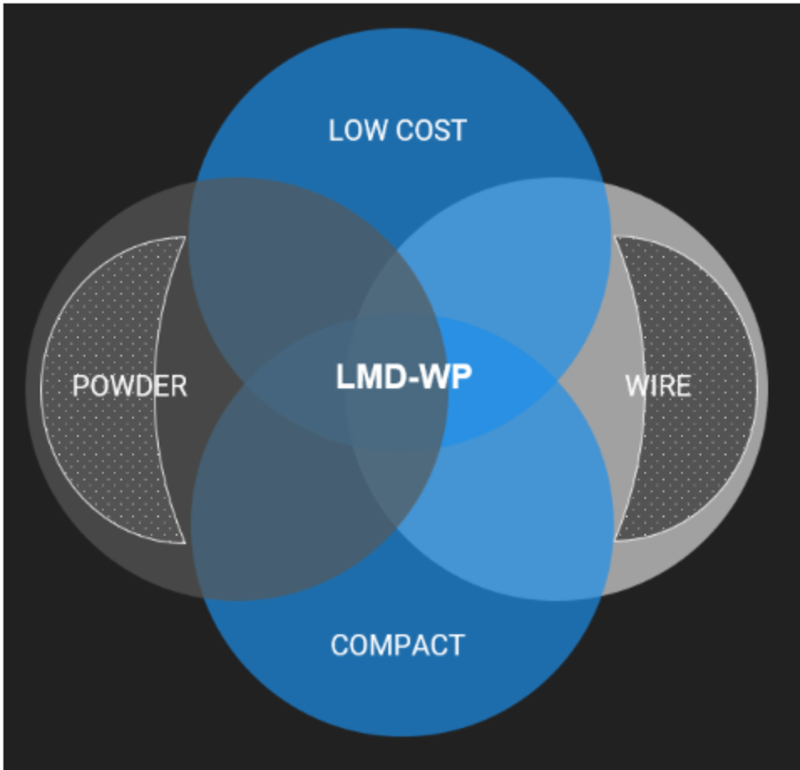
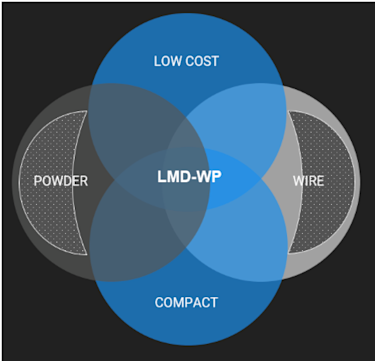
Figure 1. LMD-WP process
TheLMD-WP process works in a similar way; however, instead of having one laser beam that enters through the center of the deposition head, multiple fiber-coupled diode laser sources are used that are distributed evenly around the central axis of the head (Figure2). This frees up the central path for solid fillermaterial andallows for the unidirectional processing of common MIG welding wires. Around the wire orifice, the deposition head also features a conical powder nozzle. This way, no functionality is lost compared to conventional laser cladding heads. In addition, it is also possible to deposit wire and powder at the same time to create a new alloy of the two components.
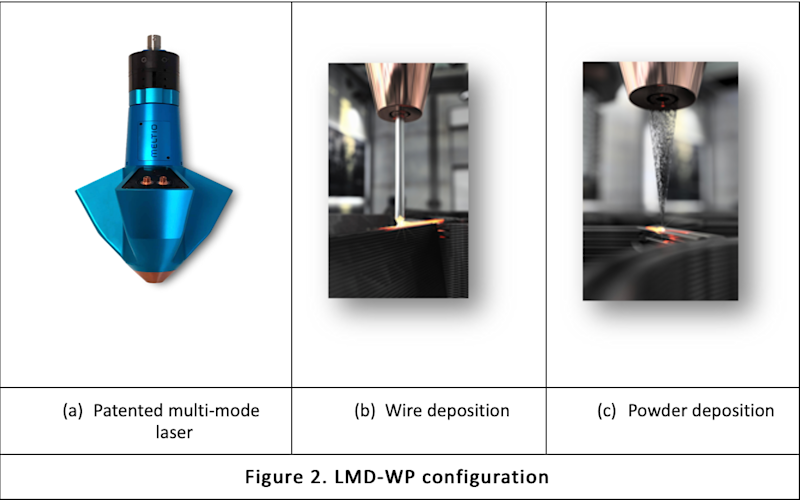
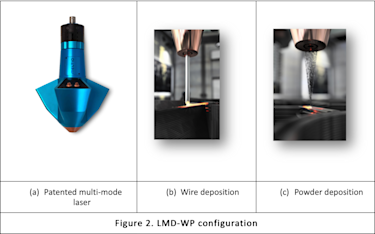
“This technology…leverages the advantages of both wire DED and powder DED.The ability to print using metal wire and metal powder independently or simultaneously without a nozzle change…is a first-of-a-kind feature in the AM industry,” explainsDr. Yash Bandari, Product Manager, Meltio. In addition, the available high laser power, multiple wire feeders, and hot wire-feed options provide high material deposition rates while retaining the precision and resolution of a laser process (Figure3). The technology can also perform other functions, such as metal coating, texturing, polishing, and cutting, without requiring external equipment.
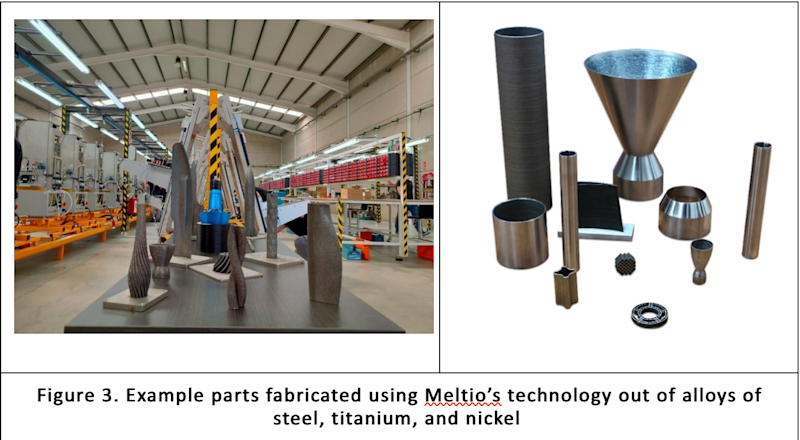
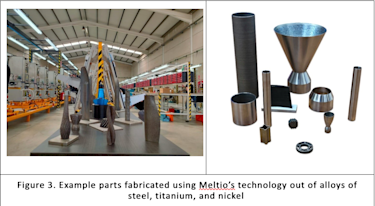
Closed Loop Control System
“Process stability was the most important aspect for the development of our printers. As wire-based coaxial deposition is not as common as powder LMD, we developed our own process control structure that not only adjusts the processing parameters on the fly, but also measures the height of the individual layers, and adjusts nozzle-to-part distance automatically,” explains Brian Matthews, Chief Technology Officer, Meltio. To grant users maximum flexibility, all process parameters can be set in G-Code. A macro utility is provided to easily change parameters for certain sections of a build. Due to this closed loop control, the print quality is very high in both the wire and powder modes (Figure 5). The printer can be controlled either via a locally hosted web interface or through USB.
Conclusion
LMD-WP technology can be used to create components from scratch, can be used for rapid prototyping, part repair, or the creation of components in any type of industry that uses metal components without size limitations. Its versatility and pricing could encourage the expansion of many companies into the metal 3D printing space in the near future.
About the Author:
Dr. Yash Bandari works at MELTIO as a Product Manager in the Additive Manufacturing (AM) group. Yash has an extensive experience in directed energy deposition (DED) processes to his current work with maturing and commercializing wire-based AM technology. He worked on electron beam additive manufacture (EBAM), wire + arc additive manufacture (WAAM), Laser + Wire additive manufacture (LMD-w) and blown powder additive manufacture (LMD). Yash received his Ph.D. in manufacturing engineering from Cranfield University, UK where he conducted research for companies like Lockheed Martin UK, United Technologies Research Center, Technip FMC etc. He also gained experience working for TATA Motors Limited in India as a technical manager in AM department; also for Oak Ridge National Lab (ORNL), where he was involved in developing a control system for Laser + Wire/Hot wire AM; and most recently for EWI, where he was a subject matter expert (SME) and managed wire-DED projects at Buffalo Manufacturing Works (BMW).