For decades supply chains have stretched and become opaque as companies chase cheap labor offshore then import products to sell in the U.S. market. But since 2010, more companies are considering U.S. manufacturing due to rising Chinese wages, (Figure 1) low U.S. energy costs, intellectual property concerns, advancements in technology, and automation. With today’s supply chain turmoil, including special tariffs on China and supply chain vulnerabilities revealed by the COVID-19 pandemic, many companies are reevaluating their China sources.
The Strength of the Reshoring Trend
In 2017, annual reshoring plus foreign direct investment (FDI) jobs reached 190,000 up from 6,000 in 2010. In 2018, the number of companies reporting new reshoring and FDI was at the highest level in history, up 38% from 2017 to 1389 companies with more than 150,000 manufacturing jobs reported. 2019 tariff uncertainty reduced the annual flow to about 110,000. Cumulative jobs created reached about 800,000, over 6% of total U.S. manufacturing employment. Now, companies are averting supply chain disaster and pivoting to the “new normal.” Priorities are beginning to shift from cost minimization to more resilient, localized supply chains and risk minimization. Reshoring is beginning to surge again in 2020 (Figure 2).
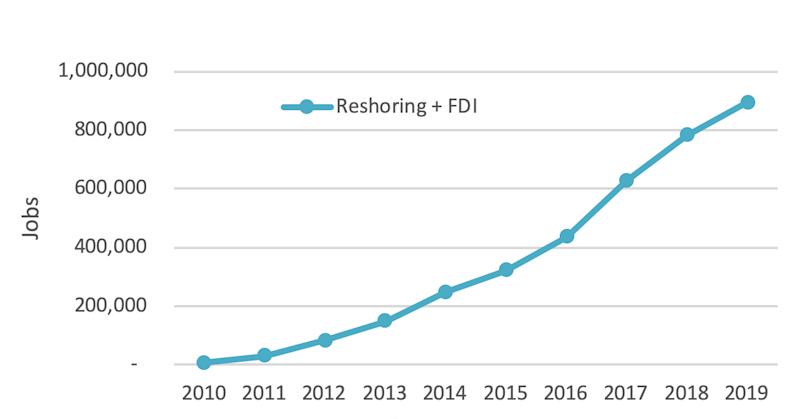
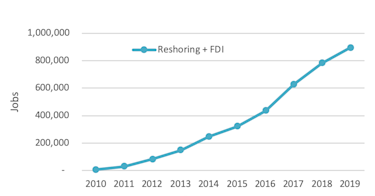
The historically strong surge in manufacturing employment for the last decade reflects the impact of a slowing rate of offshoring and a rapidly growing rate of reshoring and FDI. December 31, 2019, employment is about 3.2 million higher than would have been forecast in 2006 before the Great Recession (Figure 3).
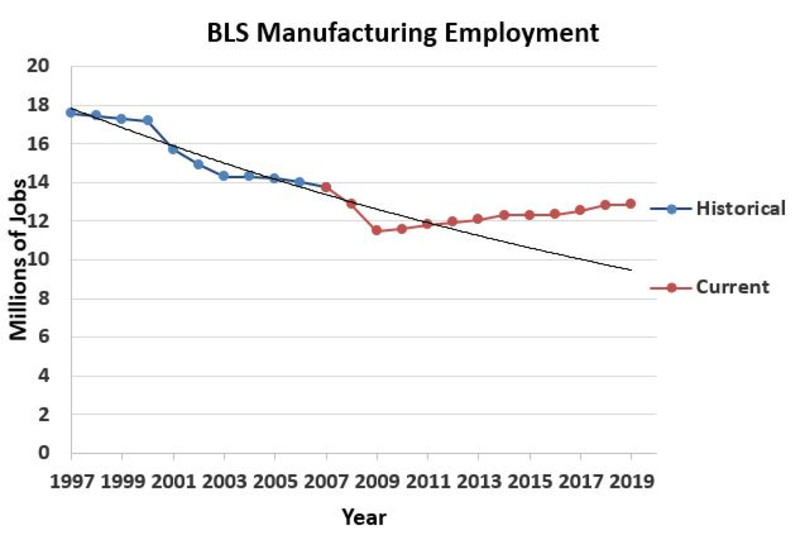
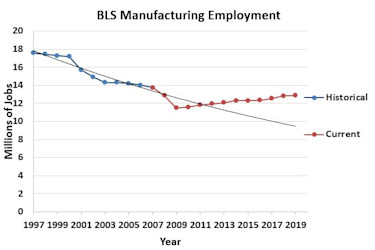
Emerging concerns and considerations The trade war uncertainty and pandemic resiliency concerns are underpinned by other concerns like environmental, intellectual property, and sustainability.
Environment Sourcing offshore is negatively impacting the environment according to “Targeted opportunities to address the climate–trade dilemma in China” by Harvard’s Dr. Zhu Liu, et al. According to the study, “International trade has become the fastest growing driver of global carbon emissions, with large quantities of emissions embodied in exports from emerging economies.” A Reshoring Initiative® study showed a +25% reduction in emissions by shifting sourcing of a 2 pound aluminum die casting from China to the United States.
Intellectual Property China remains the “world’s principal IP infringer” with an estimated $600 billion annual cost to the U.S. economy. Large companies like Apple, IBM, and GE have fallen victim to IP theft by Chinese employees. A recent CNBC CFO survey found one in five corporations say China stole their intellectual property within the last year. Nearly one-third of CFOs of North American-based companies say Chinese companies have stolen from them during the past decade.
Sustainability It has become harder for U.S. companies to make money in China. Members of the American Chamber of Commerce in China say that they are earning less, and market access is an issue in some industries. A recent study found that 50% of American technology sector companies feel they are treated unfairly. Only 61% of companies described their financial performance in China as “profitable,” the lowest in about twenty years.
Dazor Manufacturing, a global manufacturer of professional-grade task lights, desk lamps, lighted magnifiers, and digital microscopes reshored 90% of parts from China to Missouri.
Stan Hogrebe, president, found there were hidden costs associated with larger inventories, travel, freight, and noncompliant parts. He said, "After we took a hard look at all the cost variables involved, not just the quoted unit price, it made business sense to bring back a number of component parts—including our die casts, metal bending, and extrusions." Using automation and sourcing locally with Production Castings, an aluminum and zinc die caster in Fenton, Missouri, made economic sense.
E-Commerce Customer preferences for e-commerce and fast delivery put a high priority on proximity to market. QRM (Quick Response Manufacturing) and lean manufacturing reduce internal and external lead times and allow local suppliers to retain the delivery advantage provided by proximity. Expert Jim Womack’s lean message to “calculate the true cost” emphasizes the benefits of using total cost instead of price for sourcing decisions.
Recent studies show American attitudes are changing. According to a McLaughlin & Associates study, 75% of Americans felt that the United States should end its dependence on China for medical imports including PPE and pharmaceuticals. A recent Harris poll revealed that Americans thought companies should “pull back from manufacturing in China” (71%), and are in favor of tough U.S.-China trade policies (69%). I emphasize China since China accounts for about 40% of all reshoring over the last 10 years.
Investments in Automation and New Technologies Automation, a key enabler, has narrowed the labor-cost differential, reducing the offshore labor-cost advantage and making the United States more competitive. Digitization and reshoring are tightly and positively linked. Reshoring increases capacity utilization, which drives capital investment in the newest technologies. The new systems increase competitiveness, enable recruitment of a smarter tech-oriented workforce, and thus enable more reshoring. Figure 4.
Companies with shorter supply chains did better during the COVID-19 disruption The coronavirus pandemic revealed the vulnerabilities of hyper-connected global supply chains, and companies with local supply chains fared better against the disruption. For example, toolmaker Stanley Black & Decker recently shifted production of its Craftsman tools from China to Texas. It reported no increase in costs and “much less impact from the coronavirus than would have been the case if it had remained in China.”
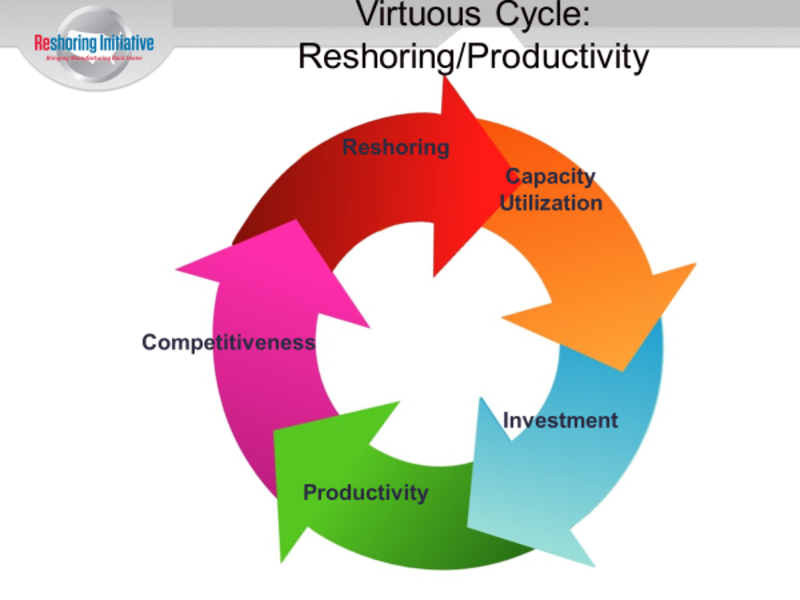
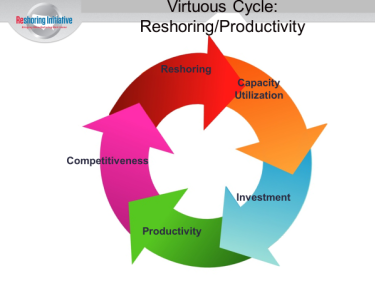
Unilever has upwards of 200 factories worldwide and kept running at about 85% capacity. Unilever CFO Graeme Pitkethly said, “Most of our supply chain is local, it’s very flexible, and generally speaking, the vast majority of the products we sell in a country, we supply in that country.”
ReEvaluate and ReEngage! Allowing for a one to two-year lag from announcement to hiring, reshoring and FDI are responsible for about 750,000 manufacturing jobs and about 6% of the current total jobs. Now is an especially good time for companies to reevaluate the choice of domestic vs. offshore production. To help with the reevaluation, the Reshoring Initiative® website provides tools to help companies decide objectively whether their overhead will come down more than their manufacturing cost goes up when sourcing locally.
The free online Total Cost of Ownership Estimator® will more accurately determine the real profit and loss impact of reshoring or offshoring. After doing the math, most companies will decide to bring some work back.
Whether you are an advanced manufacturer, job shop owner, or OEM, you are experiencing your own supply chain challenges, uncertainties, and questions. In an extraordinary effort to support you, AMT and IMTS are dedicating significant staff and financial resources to help you rethink, reengage, and reestablish supply chains. Visit www.IMTS.com/SupplyChain to learn more!
To speak with the Reshoring Initiative, email Harry Moser at harry.moser@reshorenow.org.
THIS ARTICLE WAS ORIGINALLY PUBLISHED ON IMTS BY HARRY MOSER ON OCTOBER 26, 2020.