Who wouldn’t want to get more for less? In a pragmatic sense, a technology can be considered more sustainable than its competitors if it provides more while spending less. The caveat, of course, being that for sustainable technologies “spending less” is defined more broadly than usual: environmental and social costs are accounted for alongside traditional economic considerations, and often a longer range view is taken.
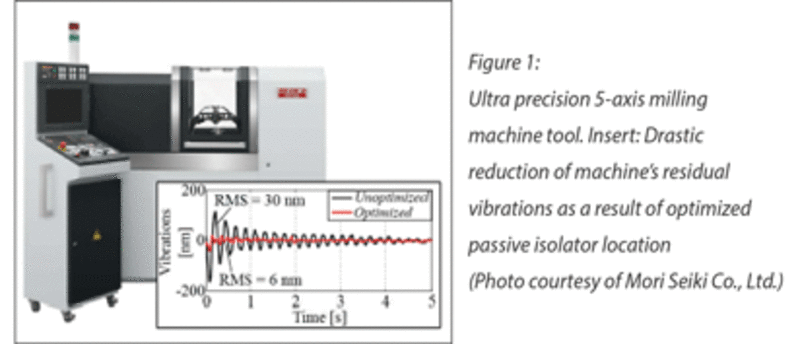
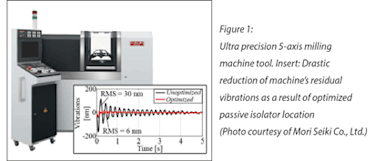
With this in mind, sustainable manufacturing technologies must aim to improve (or at least to maintain) performance while reducing economic, environmental and social costs. This goal can be achieved by investing in the development of new technologies or by making smarter use of existing technologies. The MSR lab has recently focused more on the latter. We adopt a multi-disciplinary approach that aims to make manufacturing systems smarter by exploiting built-in synergies, such that the final result is greater than the sum of its parts. From the standpoint of manufacturing machines and automation, we seek to answer the question: How can one best integrate electromechanical design, sensing, computing, controls, etc. to improve performance with minimal cost? Of course, the answer to this question partly depends on the specific application being considered, but we also seek to dig deeper and find generalizable principles that can be transferred to other applications.
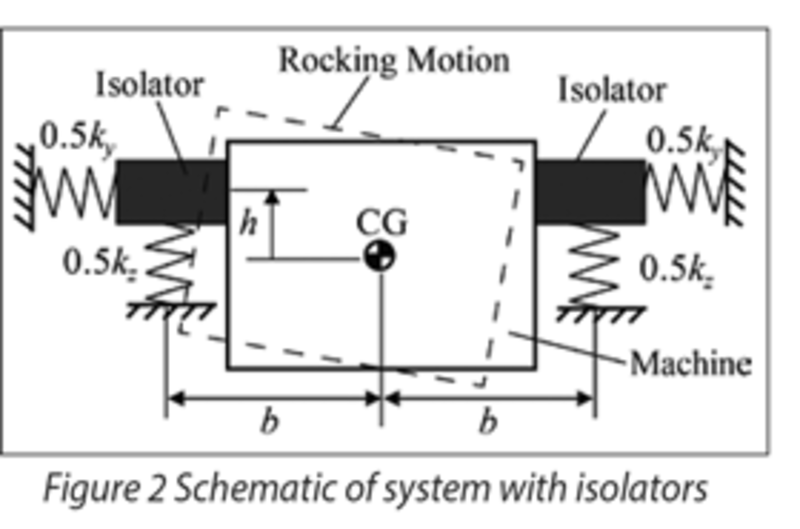
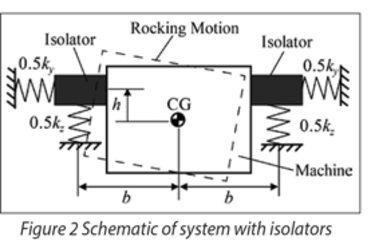
One example is our current project on low-cost, energy-efficient reduction of vibration in ultra-precision manufacturing (UPM) machines, such as micro machine tools and coordinate measuring machines. These machines fabricate and measure complex parts with microscale features and nanoscale tolerances. The resulting parts are critical to high-performance microdevices and are largely responsible for advances in biomedicine, electronics, communications and many other fields. But because of the level of accuracy required, UPM machines must be isolated from unwanted vibration, both ground vibration and residual vibration from the machine itself as it executes motion commands. Manufacturers often use passive vibration isolators to reduce vibration. While passive isolators are relatively inexpensive, reliable and don’t require energy, they are typically less effective against residual vibration. Active vibration systems, by contrast, apply energy to counteract vibration, which makes them more effective, but they also add significantly to overall costs and energy consumption. While working at Mori Seiki’s Digital Technology Lab (DTL) before joining the UM faculty, our team was charged with designing the ultra-precision 5-axis milling machine shown in figure 1 above. During experiments, we discovered that slightly changing the location of its passive isolators significantly reduced residual vibration, but we didn’t understand why. Now, as part of research supported by the National Science Foundation and industrial collaborations, the U.M. research group is trying to uncover the underlying principles behind vibration reduction as the isolator location changes. Figuring out how best to use passive isolators to achieve near-active-system-level performance would help save costs and energy without sacrificing quality and productivity in UPM machines. So far, our research has revealed that a fascinating phenomenon known as mode localization is a major contributor to the reduction of vibration we observed in our 5-axis UPM machine. Mode localization is described as a catastrophic-type phenomenon because it can cause large changes in a system’s response due to small changes in its parameters. In a passively isolated UPM machine, the height (h) of the machine’s center of gravity (CG) relative to the isolators is one such parameter. The effect of h on the machine’s rocking motion (residual vibration) largely depends on a dimensionless parameter ε defined as below:
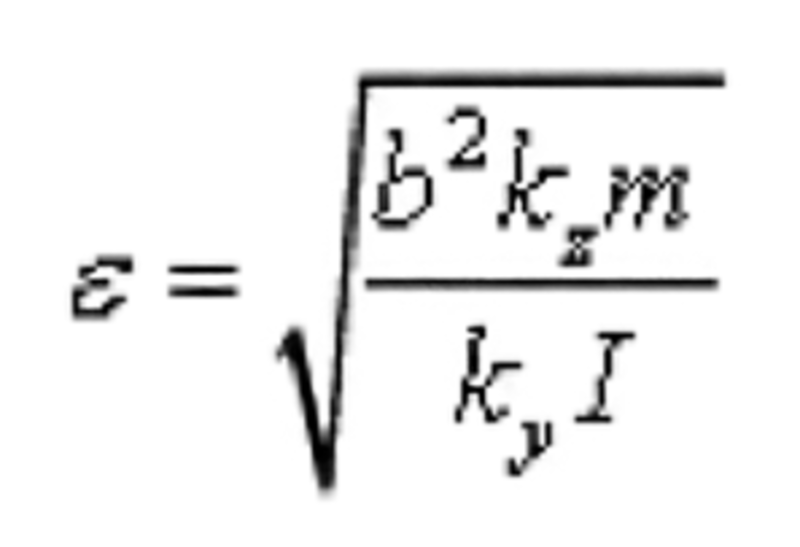
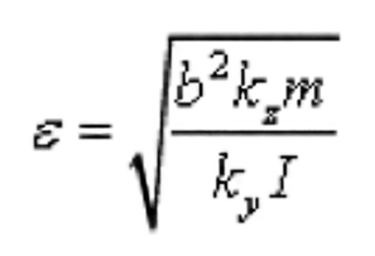
In this equation, m and I are respectively the mass and centroidal moment of inertia of the machine. ky and kz are the combined stiffness of the isolators in horizontal and vertical directions, respectively, and b is the half-span of the isolators. We have discovered that when ε < 1, slightly lowering the CG with respect to the isolators is very likely to decrease residual vibration, while slightly raising it could significantly increase vibration. Conversely, when ε > 1, slightly raising the CG generally reduces vibration, but lowering the CG a bit with respect to the isolators increases vibration. Now we know that at DTL, we were simply lucky to have fallen on the favorable side of mode localization. UPM machine designers, armed with knowledge from our research, can now be a bit more confident about when and how to reduce residual vibration. All they may need to do, as was done in our case, is to simply insert 4 cheap spacers between the machine and its isolators! In Part 2 of this article, we will describe another research project where we borrow ideas from hybrid electric vehicles to improve manufacturing machine performance, while reducing energy consumption and associated costs. Dr. Chinedum Okwudire is the Director of the University of Michigan’s Mechatronics and Sustainability Research (MSR) lab and has provided the members of AMT with a quick summary of the sustainability research ongoing in his lab. If you have any questions, please contact Tim Shinbara at 703-827-5243 or tshinbara@AMTonline.org or Dr. Chinedum Okwudire at okwudire@umich.edu.