In many ways, IFB Solutions is a lot like other small manufacturers. The corporation has three locations in North Carolina, employs 140 people with a variety of processing and assembly skills, and is ISO 9001 compliant. What makes IFB unique is that nearly all of its employees are blind or visually impaired.
Headquartered in Winston-Salem, IFB Solutions trains and employs people who are blind to work in their manufacturing facilities on government contracts for textile products and office supplies. For many employers, hiring a person who is blind may seem impossible or difficult, an outlook fueled by misconceptions about a person who is blind’s true abilities.
“A person who is blind may not be the one you want flying your airplane, but there's no reason why they can't run the airline,” says Dan Kelly, CEO of IFB Solutions. “We’ve been able to shatter most perceptions about the capabilities of people who are blind.”
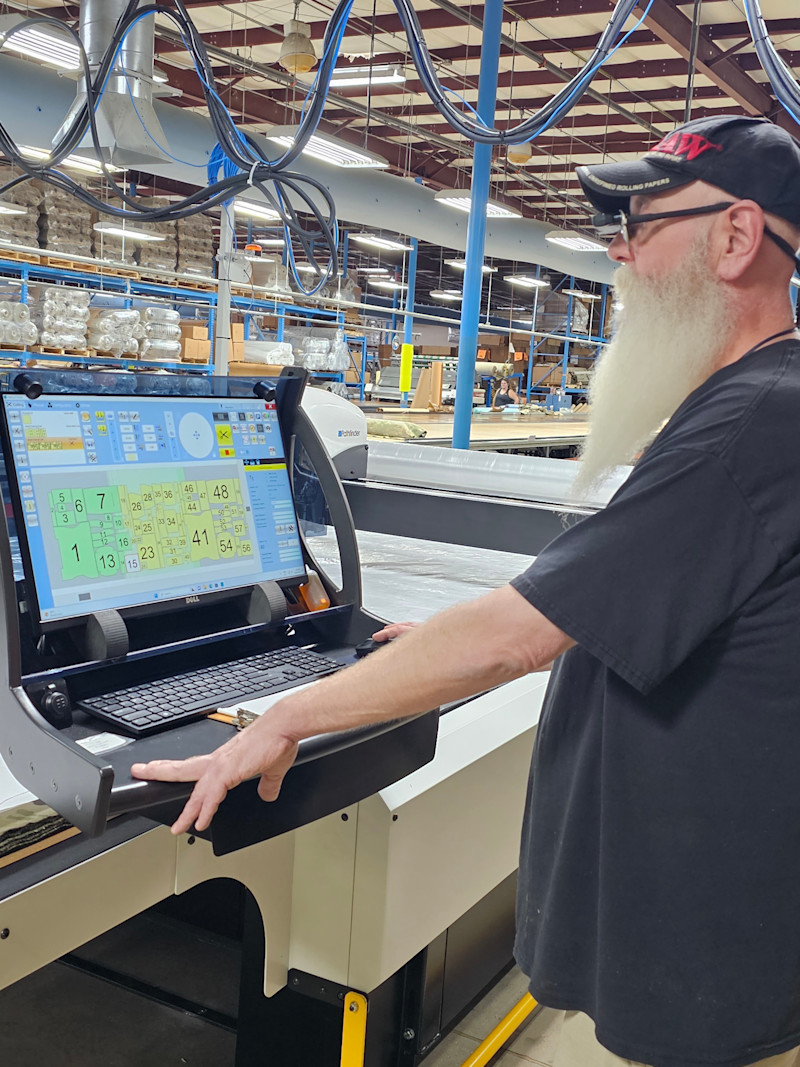
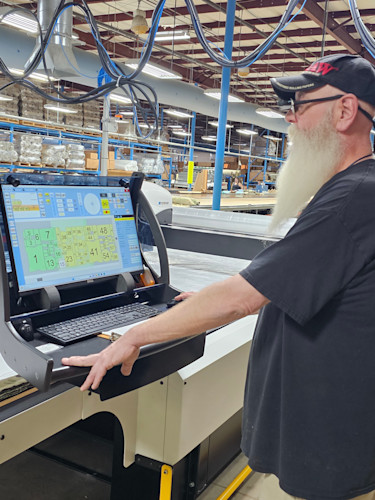
National Industries for the Blind IFB Solutions is one of the nearly 100 nonprofit agencies across the country that is associated with National Industries for the Blind (NIB), the nation’s largest employment resource for people who are blind. NIB and its associated nonprofit agencies create and sustain thousands of U.S.-based manufacturing jobs each year, producing a wide variety of finished products for government and commercial customers. Their network offers manufacturing services such as machining, fabrication, assembly, kitting, packaging, plastic injection and blow molding, chemical blending and filling, and textile cutting and sewing.
People who are blind are one of the nation’s greatest untapped labor resources. According to the Bureau of Labor Statistics, the jobless rate for those with a disability is about twice as high as the rate for those without a disability. NIB and its associated nonprofit agencies are the largest employer of people who are blind in the U.S., creating opportunities for people who are blind to build personal and economic independence.
Low Vision Not a Problem for this Machine Operator “After 40 years in aviation maintenance, I thought my work career was over when my vision was impaired, but having a job at IFB feels like a second chance because I am a productive member of society again,” says Bobby Ashworth, machine operator at IFB. “IFB open their doors despite my low vision, and it has made a huge impact in my life. I have learned that I can still be an asset to a company and that low vision isn’t a death sentence.”
IFB is contributing to the resurgence of domestic reshoring helping the local economies. IFB workers do assembly, metal stamping, and sonic welding operations for a spring-powered stapler that was previously made completely overseas. Another division makes and assembles office supplies for government and commercial customers, while the majority of the work at IFB is producing heavy duty clothing and outerwear for the U.S. Defense Department.
Simple modifications
The most common misunderstanding about visual impairment is awareness that there’s a range of impairment, from low vision to complete blindness. Legal blindness is a designation for people with a visual acuity of at least 20/200, which means that they can only see the big E at the top of the eye chart, even with corrective lenses. If the person who is blind has a lighter or moderate level of impairment, there may not be a need for elaborate job accommodations.
When a new job begins at IFB Solutions, the internal engineering team evaluates the manufacturing process and determines whether any modifications are needed to accommodate an employee with some level of vision impairment. Many modifications involve a combination of lighting, color contrasting, and magnification. Someone who’s totally blind may use a physical jig or fixture that was developed to assist with guiding a cutting, sewing, or assembly operation.
Gigi Dottin is the program director for Productivity Engineering and Technical Training at NIB. She and her team of engineers visit NIB associated nonprofit agencies to provide support. They assess the agency’s assembly process to find opportunities for blind conversions and efficiency improvement, and they recommend adaptations to enable people who are blind to perform particular jobs. For example, machines can be fitted with speech outputs or larger control screens. In many cases, the solution to make a job accessible can be something as simple as 3D printing a machine accessory or using technology that’s already on site.
“A large number of accommodations are what any other manufacturer would do in a 5S/lean thinking environment,” Kelly says. “For example, we can de-skill the operation using advanced, automated, programmable sewing machines to do set stitch patterns. Many of the jigs and fixtures we use are the same as a large operation would use for efficiency, precision, and quality. There’s often very little that is done beyond what any other company would implement.”
Dottin and her team are already looking forward to attending IMTS 2024, where they’ll learn about the latest in automation and other advanced manufacturing technologies that we can use to make job modifications for workers who are blind.
Manufacturers interested in learning more about accessible job accommodations for their operations can contact National Industries for the Blind for assistance.
Exceeding expectations
Even with America’s labor shortage, some manufacturers wonder if it is worthwhile to consider hiring a person who is blind. Dottin emphatically says, “Yes!” Through her work with NIB, she knows firsthand that many people who are blind have no trouble keeping up with a fast-past production line.
“As long as you provide good training and work with their strongest abilities, a person who is blind can do almost anything that a sighted person can do,” Dottin says. “And in many cases, they are more likely to properly follow the process and be productive.”
Learn more about hiring people with blindness for manufacturing jobs at www.NIB.org.