Tony Roma is the chief engineer of the Cadillac CELESTIQ, an all-new electric vehicle that will go into production by the end of this year.
The phrase “go into production” may be a bit exaggerated.
“Cadillac’s brand legacy was forged with hand-building the most advanced vehicles of their era,” said Roma. “We are returning to that tradition with CELESTIQ, creating a piece of automotive art with each one produced.”
The car will be built at the GM Global Technical Center in Warren, Michigan, not in a traditional factory. GM has invested $81 million at the campus to support the vehicle.
The area where the CELESTIQ will be built is called the “Artisan Center.”
While the whole undertaking is small batch (no more than six vehicles will be in production at any one time) and artisanal, GM is not overlooking contemporary tech for the vehicle, which includes some 300 approved and pending patented technologies and processes, from the tech of the propulsion system to connectivity. In the manufacturing arena, they will be using six large precision sand-cast elements (GM refers to them as “mega castings”) for the vehicle underbody, each of which is said to reduce part count by 30 to 40 components.
And it should be no surprise that they are utilizing additive manufacturing for the CELESTIQ build.
Additive Infrastructure
Building the car at the GM Tech Center is certainly convenient when it comes to additive.
In 2019 in the Cole Engineering Center, the central engineering building on the Tech Center campus, the 4,000-square-foot Additive Innovation Lab was opened. While some companies might have hidden the lab away from crowds, GM put the lab in an area with considerable foot traffic and worked to engage people who expressed interest in what was going on because there was an understanding that while additive would be important, it wasn’t something that a lot of people were familiar with. Ali Shabbir, a GM engineer who focuses on additive, described the Additive Innovation Lab as a “maker space.” With interest in the tech, there could be interest in finding new applications among the engineers who happened to walk by and see the roughly 14 machines in action.
While the Additive Innovation Lab is something of an idea generator, GM added to the site something that would put ideas into something more substantial.
In December 2020 GM opened the 15,000-square-foot Additive Industrialization Center at the Tech Center. It was equipped with 24 machines of various types, including selective laser sintering (SLS), selective laser melting (SLM), fused deposition modeling (FDM), and Multi Jet Fusion. Here the objective is, as the name implies, the productionizing of the processes. Shabbir said that what they want to do is “find a home” for the equipment in manufacturing facilities throughout the GM organization, places where the equipment can be applied.
An example of the benefits of rapid prototyping: The process was used to develop brake duct designs for the Corvette C8, and it took nine weeks’ time and 60% of the cost out.
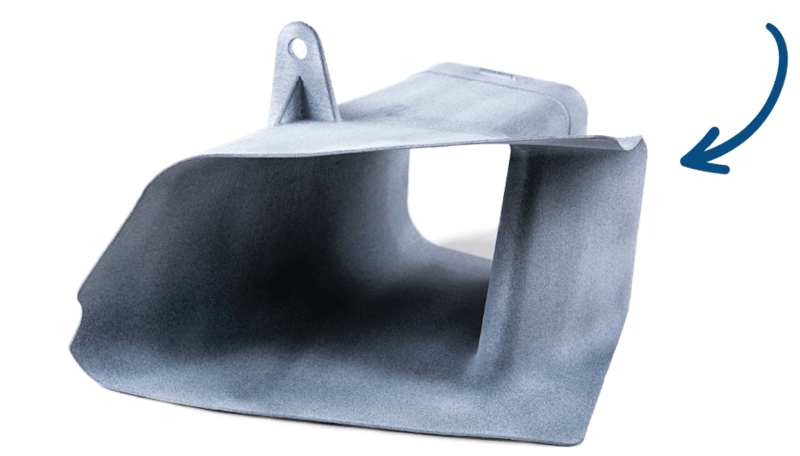
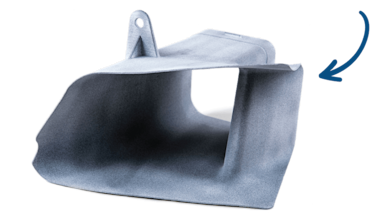
(Image: Steve Fecht for GM)
‘Rapid Prototyping’
Like many companies in industries from aerospace to medical devices, GM has been using 3D printing – a term used for the prototyping stages (which explains why there is also the synonymous term “rapid prototyping”) as distinct from additive manufacturing (which is more serial production) – for a number of years.
A good example of this – and also good because of the car in question – is the development of the brake cooling ducts for the C8 Corvette. GM found that by using 3D printing during development, the timeline for obtaining prototype parts was reduced by nine weeks, and the associated costs were cut by 60%.
Which goes to the point that although there is now more focus being placed on additive manufacturing than rapid prototyping (probably because the former is still comparatively new, and rapid prototyping goes back to the late 1980s, when the process started being commercialized, albeit to a limited extent), there is still a significant amount of time and money that is saved during the prototyping phase of product development – and it has serious ramifications on what will be developed.
(And here’s something to keep in mind: It very well may be that whatever is being prototyped using one of the 3D printing processes may be designed in such a way that the item can’t be as effectively or efficiently produced by more traditional manufacturing processes (e.g., machining, molding) – if it can be produced by those processes at all.)
So, for the CELESTIQ, there is an abundance of additive near the Artisan Center.
GM’s Biggest Additive Deployment
According to Roma, there are 115 parts made with additive for each CELESTIQ. There is no other car in the GM lineup that has nearly that many.
It is worth noting that the first production applications for additive at GM were for the 2022 Cadillac CT5-V Blackwing and CT4-V Blackwing models equipped with six-speed manual transmissions. There are four parts. Three are functional: two nylon-12 HVAC ducts and an aluminum bracket that is used to secure a wiring harness. The fourth part is a stainless-steel badge that’s affixed to the top of the gearshift knob.
For the CELESTIQ there are a wide array of parts, including window switches, grab handles, decorative interior pieces, and vehicle structural elements. The steering wheel center has a decorative front side and a structural reverse.
Safety Critical
One of the more interesting components that might be overlooked but shows the type of advances that are being made at GM is the D-ring that is used to position the seat belt. Seat belts fall under Federal Motor Vehicle Safety Standards (FMVSS) as regulated, safety-critical parts of a motor vehicle.
Roma recalled, “When they [the additive team and the safety team] came to me, I had the reaction: ‘You want to do what?’” The stainless-steel component was developed. When the teams tested the ring to failure, they discovered that it would have been capable of supporting the entire vehicle “and then some.”
While GM has yet to share specs of the imposing vehicle, this is a large electric vehicle. Electric vehicles tend to be heavier than those powered by internal combustion engines. Lucid Air’s Dream Edition Performance sedan has a curb weight of 5,812 pounds; the GMC HUMMER EV SUT pickup truck tips the scales at 9,640 pounds. Whatever the weight of the CELESTIQ, evidently that additive part has excellent performance characteristics.
But There’s This
There are two things to know about the CELESTIQ that we’ve kept until now:
The vehicle will have a starting price in the realm of $300,000. Roma said that because this is a hand-built model, customers will be able to have levels of personalization and customization that have heretofore not been even considered. Those choices will certainly have an effect on the price of the car. Conceivably that $300,000 is simply a placeholder that will soon have several significant digits added to it. The Artisan Center will build no more than six vehicles at any one time. These cars will be built to order. You won’t drive by your local Cadillac dealer and see several parked on the forecourt. Even though this is a production vehicle, the volumes are comparatively small. Perhaps the best way to think about this is to know that in 2022, Rolls-Royce Motor Cars delivered a record 6,021 vehicles globally. And Rolls-Royce has an entire factory dedicated to its vehicles, including a highly popular (comparatively speaking) SUV. (Rolls-Royce’s first use of additive was for the Ghost Extended model launched in 2020; it used beam melting, Multi Jet Fusion, and selective laser sintering.) But Roma made a point about the use of additive for the CELESTIQ and what it means more broadly to GM: “This will help open our manufacturing team’s mind to what’s possible.”
He believes that when it comes to deploying additive, there will be an exponential curve, going from hundreds of parts to tens of thousands.
The Importance of Tools
But there is another place where additive makes a difference. Roma said that they are also using it for producing tools like check fixtures and assembly fixtures. He said that these tools can otherwise cost tens of thousands of dollars. Again, both cost and time are saved by making the tools with additive.
Tools and fixtures are applications that GM is using additive for. Not only are there time and cost benefits, but by being able to make them with polymers rather than metal, they can be significantly lighter than metal versions.
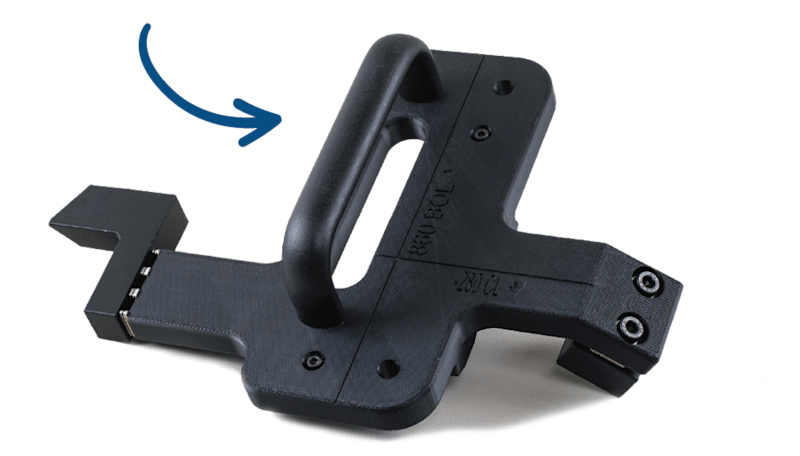
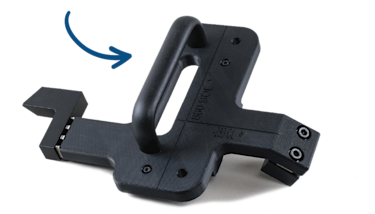
(Image: Steve Fecht for GM)
And there is another important factor: Ergonomics. Sticking with Cadillac: The Escalade is produced at the Arlington Assembly plant in Texas (along with GM’s other full-size SUVs, the Chevy Tahoe, Suburban, and GMC Yukon). To prep the plant for production of the current-generation vehicles, GM invested approximately $1.4 billion in the plant, everything from 1,450 new robots to laser scanners to precisely locate the positions on body panels where piecing is required for assembly.
But another thing that they did was use additive to produce some 100 different tools used in the plant. Previously, these tools were made with aluminum. And while aluminum is light, a given tool that is handled by a worker would weigh between 10 and 40 pounds. It wouldn’t take too long before “aluminum is light” would seem an absurd statement.
So, using a nylon carbon fiber composite, tools are made that weigh a more manageable three pounds.
Roma has been at GM since 1993. He’s had a variety of roles, including race engine team manager for the Cadillac CTS-V racing program. He’s worked on the Camaro, Corvette, GTO.
So, when he says of additive, “It’s exciting stuff,” it is clear that this is something that is more than a run-of-the-mill addition to the design, engineering, and production tool set.
If you have any questions about this information, please contact Gary at vasilash@gmail.com.